R-22 is an HCFC (Hydrochlorofluorocarbon) refrigerant found in older commercial and residential HVAC equipment, such as RTUs (roof top units), split systems and other equipment. R-22 and other HCFC refrigerants are known to deplete the Earth’s protective ozone layer and contribute to harmful climate change.
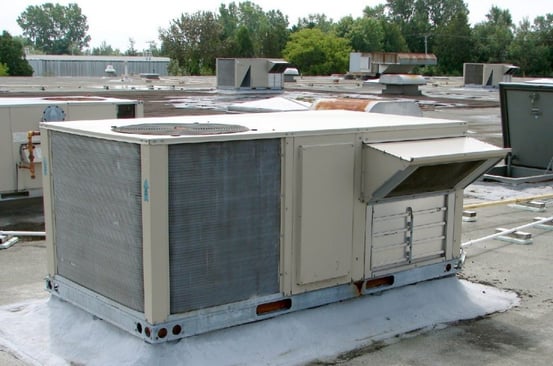
The United States has slowly been phasing out the use of R-22 per the following phase-out schedule:
- 1/1/2010:
The US government banned the use of R-22 in new HVAC equipment. - 1/1/2015:
The US government bans the production and import of all R-22 - 1/1/2020:
The US government will ban the use of all R-22 (with a few exceptions). This will be the end of the road for R-22 use in the U.S.
NREL (National Renewable Energy Laboratory) estimates 40 million commercial RTUs were installed in the U.S., in the decade prior to 2010. The U.S. Department of Energy also estimates that at least 1.6 million old, low-efficiency RTUs are in operation in the U.S. This means there is a huge tidal wave of R-22 equipment in operation that will need to be replaced in the very near future.
How does the 2020 ban affect me?
R-22 costs have skyrocketed and are already more than 4X the cost/lb. of R410A. Older R-22 units have much lower EER ratings and are as much as 50% less efficient than current-day high-efficiency units. In most cases, older R-22 RTUs cannot be converted to R410A refrigerant, and the older units will need to be replaced with a new, more energy efficient, more environmentally friendly RTUs. It is
already cost prohibitive to repair older R22 units, and the “fix-on-fail" emergency replacement philosophy will be MUCH more expensive than a pro-active roof-sweep or planned equipment replacement program.
How can I best prepare for the phase-out, and where should I start?
I recommend companies start with an HVAC inventory of their older equipment. Hire a firm to conduct a detailed survey of all their facilities to verify the age and condition of all HVAC equipment, including newer and older HVAC equipment. For the firm, I recommend involving a national or regional HVAC installation partner, plus an independent, national testing, balancing & commissioning partner such as Melink Corporation to provide the unit data and a complete assessment of the entire mechanical system. The survey should include ductwork inspections, inspection of the RTUs, and exhaust fans. Additionally, air-flow measurements should be recorded to verify proper building airflows and identify existing air balance issues. If the entire HVAC system is not inspected, the building will often continue to have comfort problems and building balance issues, even after the new equipment is installed. The positive effects of the new, energy efficient HVAC equipment will not be fully realized, resulting in a lower-than-expected ROI.
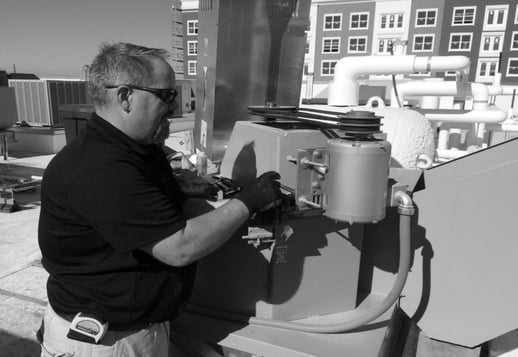
For further information on HVAC surveys and other custom scopes of work, please e-mail TBestimating@melinkcorp.com, call us at (513) 965-7300, or leave a comment below.
Contributed by Sam Rayburn